Processes & Resources
Powder Metallurgy (P/M) is the ideal process for
manufacturing durable, complex mechanical
components such as gears, cams, sprockets
and other multilevel parts.
Powder Metallurgy
Powder metallurgy (P/M) is the ideal process for manufacturing complex mechanical component gears, cams, sprockets and other multilevel parts.
The greatest advantage of the powder metallurgy process is the precise control it gives engineers over materials and their properties. From powder selection through purchasing to mixing, each blend is under strict quality assurance.
Powder metallurgy is flexible. With nearly unlimited combinations of properties, it is likely that a powder metal part can be designed to fit your application. Often, one P/M part can replace two or more existing parts, giving greater strength to the assembly while reducing inventory and manufacturing costs. The powder metallurgy process offers a lower cost per unit (due to mass production), net or near-net shape of finished pieces, and less material loss than conventional machining.
Facility
Our location in Jamestown, Tennessee, between Nashville and Knoxville, situates us in the heart of a growing industrial South. Near major transportation networks and within 24-hour delivery of 75 percent of the United States P/M market, we are prepared to supply our product to both domestic and global customers.
Equipment & Engineering
Micro Metals has a complete plant, including pressing, sintering, heat/steam treating, secondary, tool room and inspection equipment.
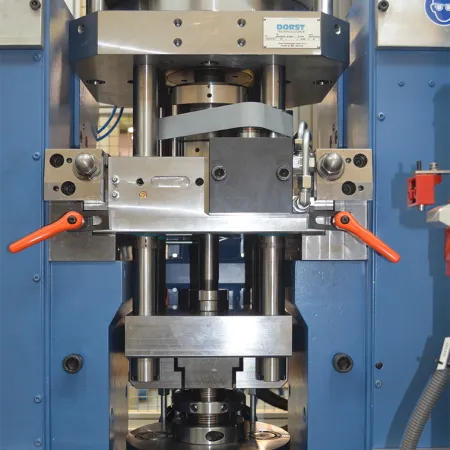
Pressing
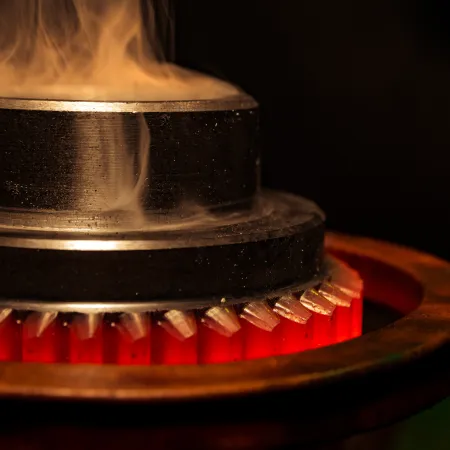
Sintering & Heat Treat
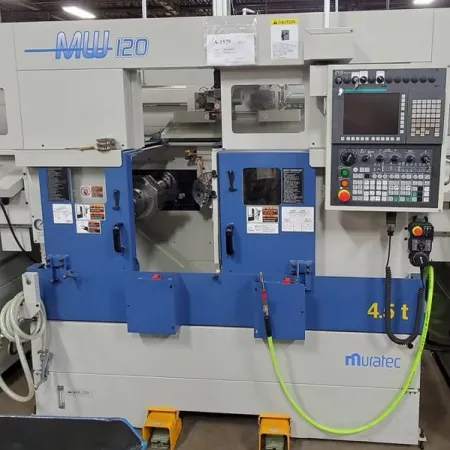
Secondary
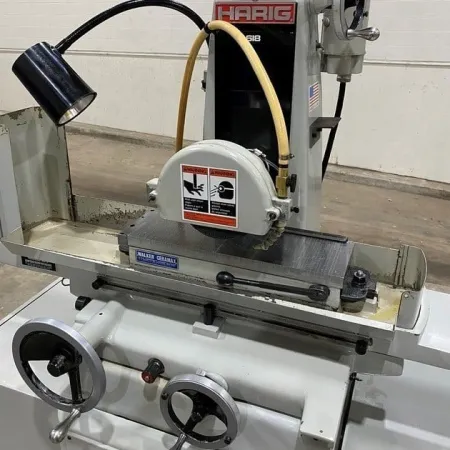
Tool Room
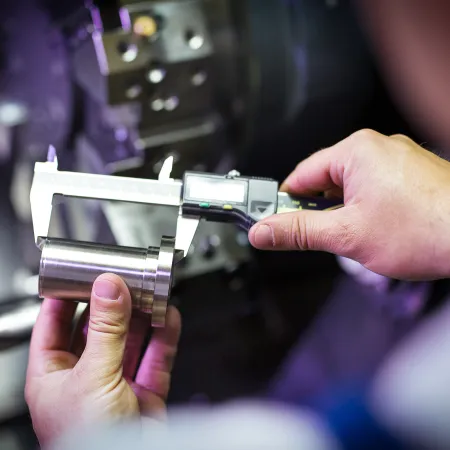
Inspection
Engineering
The customer of today demands suppliers that can provide them with the technical support required by a world market. Micro Metals stands ready to assist you in engineering a powder metal part to meet your needs by recommending suitable materials and appropriate part configurations, tolerances and processing. After the material and dimensional parameters have been established, our staff will design all tooling and fixtures while producing the pertinent FMEAs, control plans and PPAPs utilizing the latest-generation 3-D CAD software.
-
Enginnering Software – Autodesk Inventor with 3-D / 2-D Auto Cad
-
PQ Systems - SQC Pack and Gage Pack
-
Steam Treating
-
Bar Coding
-
Lean Initiative
-
JIT System
-
Powdered Metal Part and Process Research, Design, and Development Support
-
Research, Design, and Development Support for Prototyping, Tooling, Gauging, and Fixtures
-
Innovative, Efficient, and Responsive Service to Meet or Exceed Customer Requirements
-
Pull System
-
Kan-Ban System
-
Full EDI System
Tooling
Micro Metals has a fully equipped, in-house tool room that allows us to build original tooling, conduct repairs and provide any customer-required modifications. This department is staffed by craftsmen who have completed the four-year, federally accredited Tool and Die Makers Apprenticeship program. The program is conducted with the guidance of the Department of Labor's Bureau of Apprenticeship and Training.
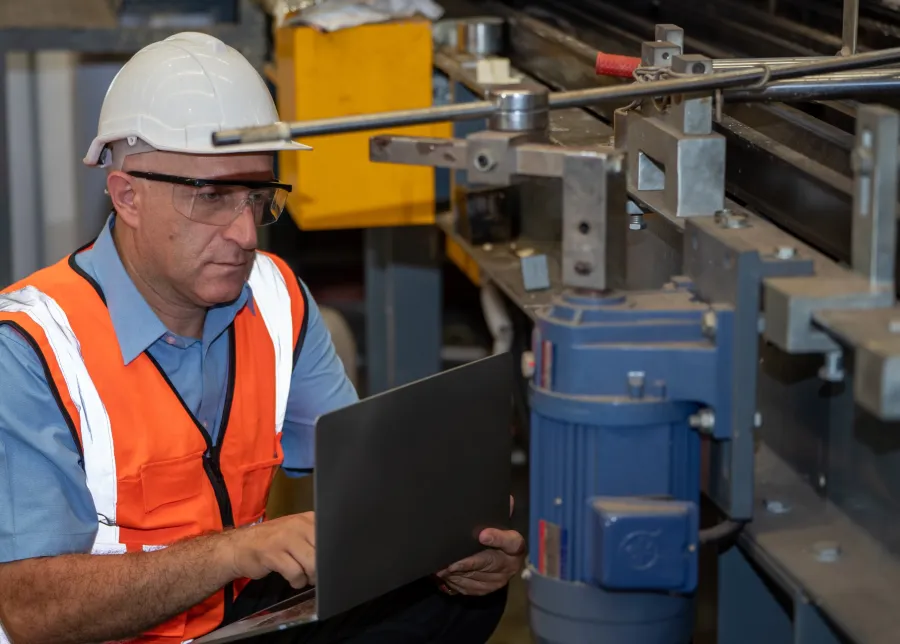
Preventive Maintenance
The quality of our product and the safety of our employees depend upon well-maintained equipment and safe surroundings. In accordance with QS standards, Micro Metals maintains an aggressive and documented preventive maintenance program.
This computerized system tracks all past maintenance and repair records and schedules work orders for future routines. In addition, it tracks the use and economic order quantities of consumables (i.e., fluid, filters, belts).